Sign In
Send us your logo
Testimonial
Read More
Client Facilities
Free Registration
Free Edits
Free Quotation
12 Hour Turnaround
Sewout With Order
Customer Support
Secure Payments
Reasonable Price
100% Satisfaction
Find us on

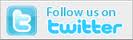
Detail
Appliqué Embroidery:
When you download an appliqué design, you'll find two files: a die line (which begins with the letters DL) and the full embroidery file (which begins with the numbers 25). You'll use the die line file to cut the appliqué fabric to the exact shape for the embroidery. You won't sew the DL file on a garment - you'll just use it to cut the fabric.Begin by opening the die line file in your embroidery software, and printing it.If you don't have embroidery software, or cannot print from it, then you can sew the die line file to make a template. To do this, hoop a piece of paper.Load the die line file into the embroidery machine and embroider that file. You can use an unthreaded needle, and the needle will perforate the paper. For the example to the left, there is thread in the needle. A die line is a simple running stitch outline, so it only takes a moment or two to sew. Once the die line file has finished sewing, set the paper aside and prepare your appliqué fabric.You can use almost any fabric for appliqué. We're using lightweight cotton, so we are backing the fabric with one piece of cutaway stabilizer. Spray the stabilizer lightly with adhesive. Smooth the appliqué fabric on top.Spray a bit of adhesive on the backside of the paper template, and smooth that on top of the appliqué fabric and stabilizer.Then, cut the shape from the fabric and stabilizer "sandwich."Remove the paper template from the fabric and stabilizer (sandwich). If you are planning on using the appliqué design again, you can store that paper template with the color change sheet for a future use. Next, back the garment with stabilizer. Hoop both fabric and stabilizer firmly. Begin embroidering the design - the full embroidery file, the one that begins with the numbers "25." This file consists of three main parts. The first part is the die line. This running stitch outline traces the shape of the appliqué fabric.Once the die line has finished sewing, spray the backside of the fabric and stabilizer "sandwich" with adhesive. Place the appliqué piece in the sewn die line.Continue embroidering the design. The next thing to sew is the tack down stitch. This is a zigzag stitch which binds the appliqué fabric to the garment. You’ll also see a satin stitch border sew. This gives the appliqué fabric a nice, smooth seal. The appliqué design might have other elements that embroider, too. This bunny has ears, eyes, nose, and a tail. You'll find the color change sheet is helpful when embroidering, as the fields are labeled with convenient descriptions. Appliqué embroidery is a wonderful way to add your favorite fabrics and patterns to your embroidery. Let your imagination run wild!
(Note: you can choose almost any fabric for appliqué embroidery. If you're working with a high-pile fleece or fur, it may be necessary to trim the nap at an angle (angling inward) after the shape has been cut to avoid fuzz peeking through the satin stitch border).
Cap Embroidery:
Embroidering hats. It can be easy and fun with the right tips and techniques so let’s get started on the subject of cap embroidery.
Are you getting a professional, crisp result when you machine embroider on caps? We’ve all had a problem from time to time getting the design to lay nicely on the front or back of a cap but with a little knowledge you will soon be putting out the perfect production with half the stress and in half the time. When we talk about embroidery on hats, it is usually in the context of embroidering using a standard or wide cap frame. The designs are usually digitized from the center working out to the sides and from the bottom of the design (closest to the bill) up to the top of the cap. If the design you are machine embroidering is high in detail, it’s best to work it in segments, working out from the center. If you follow this technique, there is less chance of design distortion. While there will always be movement when sewing a cap on a tubular frame, working from the center out should keep it to a minimum. Backing is also important in reducing design distortion. It serves to decrease the movement in the frame, and in doing so improves design quality. Try not to be skimpy on the backing. A nice long piece to reach from side to side will help to stabilize the cap in production. These are the frames that require the most specific digitizing in order to minimize the amount of movement within the frame and, consequently, the amount of distortion. Embroidery on the back of caps is usually placed on an arc and sewn in a flat frame. Although some embroiderers sew cap backs on a standard cap frame, it doesn’t hold the cap as firmly as a flat frame. When sewing flat, the frame that I use is a round 12mm frame, and the letters are placed on a 3-inch arc. New clamping frames have hit the market, which are specifically designed to tightly hold the cap during this process. They really save time and effort and should be considered.Where the 5-panel cap, the one with a solid front, is the easiest to embroider on because you don’t have to deal with the seam in front, it is the least in demand. Old fashion is what I hear from most of my cap customers. The 6-panel cap is the most popular and the structured (the one with support in the front) 6-panel cap is the most popular in my store. Working with the 6-panel cap may be a challenge in itself because of the seam in the front. If it posses a problem with your design, add a column of zigzag stitches in the front where the seam will fall and that should hold the design up and out of the seam. You will want to put a new, sharp (as opposed to ball-point) needle in each color needed for any cap embroidery because of the thickness of most hats. This will reduce the number of thread breaks and keep your letters crisp and neat. The head wear market is constantly changing; new products are being added as other products are retired, all in an effort to keep pace with the ever-changing fads and fashion. Adding these products often requires a quick course in framing techniques and new products. Make sure you keep up on changing products, accessories and framing devices because these are the tools that prepare you and keep you ready to tackle the new challenges constantly coming your way.
So from one embroiderer to another, “Lets put ââ‚.....
PUFF EMBROIDERY:
Foam or puff embroidery is done by using 4mm or 6mm special foam and trapping it inside a letter.
The needle penetrates the edges resulting in the foam being cut. The only real concern is the top of the satin stitches. Like the top of the letter "I" or the ends of the letter "T". Because there is no needle penetration at the ends of a column or satin stitch, there is no cutting action.This is what I do:
1) Put the foam down. You can even just hold it by hand in position until the first stitches trap it. Needs to be over cut or larger than the letter / word
2) Set density column and arc column to 1.0
3) Digitize the entire letter but be slightly in on the edge. Or your digitizing a slightly smaller letter.
4) Then go to the ends of the satin stitch and manual put stitches in at 1-2mm. Really what your doing is just cutting the foam by using small stitches at those ends. If you are doing a script B, you would probably not have open ends but pointed ends which would not need these small stitches.
5) So now you have a letter that is stitched loosely. The foam should now be pulled off around the edges. If you can't that’s okay and leave it.
6) Now digitize the word again with .4 densities exactly around the letter.!!!...!!!
Chenille Embroidery:
Chenille, French for caterpillar or fuzzy caterpillar, Webster’s says "a soft tufted silk, cotton, or worsted cord used in embroidery or for fringing." In North America chenille is most commonly recognized as the emblems and letters sewn on lettermanââ jackets. Historically chenille has had many uses in fashion and furnishings, from delicate work of lace to the bold look of school mascots, chenille is a form of embroidery most of us recognize.Delicate Chainstitch Lace Traditional School Mascot Moss/Chain WorkOriginally produced by hand stitching, the production of chenille became industrialized about twenty years after the patenting of the lockstitch sewing machine. A French engineer named Bonnaz invented the first chenille sewing machine in 1866, soon he joined with the Cornely Company to manufacture and market his invention. A few years later Singer received the US Patent. Since the original machine very few design changes have been made. Some models added braid or cord, but the basic machine has remained the same for well over one hundred years. Today hand operated chenille machines are made by a number of machine manufacturers. These machines are widely used by skilled operators.Chenille machines typically produce both chenille stitches, also known as moss stitches, and chain stitches. Using a hook needle that pulls the thread up from the looper below the needle plate as opposed to a standard sewing needle with a threaded eye, the chenille machine typically uses only one thread for both types of stitches, moss and chain.Stitch Formation Diagrams Chain Stitch Formation Moss Stitch (Chenille)
Chenille machines typically produce two different stitch formations, the moss stitch, which is a loop stitch and the chain stitch. Moss stitches are most often used to fill in areas and create depth, while chain stitch is used to outline, monogram and can be used to produce a more delicate look. Chenille machines, both manual and current electronic machines can use a variety of threads and needles sizes to produce vastly different appearances.The first picture shows delicate lace work using an electronic chenille machine; the chainstitch is used with fine thread and needle to produce this type of work. The second picture uses a heavier wooly type of yard to do both moss (orange) and chain (yellow).Cornely and other manual chenille machine manufacturers developed a wide variety of machines based on the original design. Machines for taping, cording and sequins as well as machines with two needles for four thread stitching! Chenille bedspreads and bathrobes are made on the same principal as chenille embroidery; the material is made on a special type of loom, as are many carpets. Chenille has been produced on Schiffli machines using a specially designed attachment and no bobbin; other Schiffli attachments also produce cut chenille.Variations of chenille are produced on multihead machines using special attachments and slub yarn, using machines like the Tajima TMLG.
The first picture shows a type of looping work done on the TMLG. The second picture shows embroidery produced on the TMLG using slub yarn.Still other deviations of the chenille look are made on various lockstitch machines by sewing down a looped yarn or cord using special attachments, commonly known as the Omni Stitch. Tajima offers the KB-2M attachment for standard lockstitch embroidery machines to produce looping. The KB-2M looping/cording device is shown in the first picture. A close-up of looping can be seen in the second picture.While there are a wide variety of methods to create a look that resembles chenille, none are true chenille embroidery. True chenille embroidery is made with a closed loop, in a moss stitch formation using a continuous yarn being worked into the material and then raised in a loop or pile. (See moss stitch diagram above).Using highly developed hand, eye and foot coordination, the skilled operator uses the right hand on the handle under the bed of the machine, the foot to operate the start/stop and machine speed and follows a pattern stamped onto the goods. A simplified explanation of the machines walking action, the foot and nipple work with the nipple holding the goods when the foot is raised then the foot coming down as the nipple is raised and the foot moving the goods. All the while following the pattern by turning the handle and guiding the material with the left hand. Called the "Universal Movement", the chenille machine created by Mr. Bonnaz was the first to use this type of movement and remains one of the only machines in embroidery or sewing that will feed in any direction.
Threading the Singer Chenille MachineWhen the embroidery industry began the move into electronic multihead lockstitch embroidery machines the mass production of chenille was left to the skilled operators manually producing chenille products as they had for years. In the late 1970’s and early 1980’s as more electronic controls were applied to lockstitch embroidery a number of embroidery machine manufacturers began "electrifying" chenille machines. Mass production and less skill were among the goals, chenille in North America was fairly expensive, and being produced one at a time. Unfortunately it wasn’t the happiest of marriages. Many of the functions of the machine were still controlled manually, raising the needle to produce a higher moss loop or a looser, broader chain; trimming the threads with the operator using a hook shaped tool were still performed manually. The results produced variation from one head to another and required more skill and understanding of chenille machines.
Tajima determined an electronic head was needed. They developed a machine to "sew by wire". Instead of using the mechanical movements found in the original chenille machines, Tajima designed a machine with various mechanical functions controlled by pulse motors. Looper drive, Z-axis drive (needle and looper synchronization), and ATH (automatic thread trimming) were now driven by pulse motors. With the pulse motors driven by electronic data the machines could produce more and produce it more accurately than ever before.Tajima CE model lubrication diagram
With the development of the new electronic chenille machine, Tajima went on to create the first automatic color change machines, using a system of multiple loopers as shown in the picture above.Traditionally patches and emblems have often utilized multiple types of embroidery, moss stitch, chain stitch and standard lockstitch embroidery are often all combined in the same work. Creating the world’s first electronic mixed head type machine, Tajima brought the chenille embroidery industry into the same realm of production as standard computerized embroidery has known for a number of years.The first picture shows close up detail work from the clown picture done on a mixed type machine, a combination of standard lockstitch embroidery, moss stitch and chain stitch are used.2 head mixed type Tajima CE machineEven today with the "electrifying" of chenille, the industry is not generally understood by many owners and operators of standard electronic embroidery machines. The electronic chenille market has not developed as quickly as the standard lockstitch embroidery market did. As embroiderers’ customers become more familiar with seeing chenille work the market is slowly coming around. Currently many owners of chenille manufacturing have skilled operators who are very efficient for small orders and the cost of moving into electronic chenille equipment is intimidating. The other prime deterrent has been digitizing, or the creation of the designs for electronic chenille machines.Until very recently the thought of creating designs for chenille was foreign to many digitizers. Electronic chenille machines were few and far between; learning to create designs for chenille appeared to be a whole new process. In reality digitizing for chenille is easier than digitizing for standard lockstitch embroidery, mostly because the North American market generally uses a heavier thread, as seen on letterman’s jackets. Because the look is bolder and the thread is heavier, chenille machines do not generate small intricate designs. Quarter inch letters will not be successfully produced on a chenille machine with these types of threads; the machines are not designed for that type of work (although finer thread and needles are available and fine work can be created). Areas are filled in quicker; registration variations are broader, making most chenille digitizing less painstaking than standard lockstitch embroidery digitizing. Recent developments in the embroidery digitizing software market has made available some very sophisticated and easy to use software just for chenille work. The industry "standard" of chenille fill areas being done in a "swirl or rosette" pattern has been computerized by the latest software, removing what was considered an obstacle in early electronic chenille mass production. Instead of filling areas in a grid pattern that some experienced chenille users objected to, software now allows areas to be filled in more traditionally, and, most importantly, very easily.Fine work can be done as well as the traditional bold look, it can be mass-produced with less skill and less variation from piece to piece.Software and electronic machines designed for the chenille market mean only one thing, more and more consumers will be looking for this type of work from their local embroiderer. As the public becomes more accustomed to chenille on an everyday basis, the market will continue to grow. Manufacturers like Tajima will continue to develop and improve their products to help embroiderers meet their customers’ demands. With innovative options like the Cording and Taping Device for chenille machines, true chenille machines controlled by electronics, and software designed to produce beautiful chenille work, Tajima will continue to be a leader in the embroidery industry.
CE machine options10 head mixed type Tajima CE machineFor more details on the Tajima CE series, click here.
What is StitchTuft?
StitchTuft is a new look in the textile industry. It is an extremely soft pile made of countless small hairs of yarn placed side by side.
How is StitchTuft manufactured and which machine is used?
We named the new machine TuftMaster, as under technical aspects the process resembles tufting which is known from carpet production. The StitchTuft is applied on the fabric to be finished by means of a special machine which looks like an embroidery machine.
How does the StitchTuft process work?
Compared to traditional embroidery, StitchTuft is not prepared on the visible face of the fabric but on its backside, i.e. the embroidery material must be placed on the TuftMaster with the future visible side pointing to the bottom. The embroidery head, as usual, moves the yarn through the fabric by means of the needle. But the loop which - like in normal embroidery - develops on the backside, is not connected with the lower thread but cut by means of a cutter. In this way, two small "pins" or "hairs" develop by each cut. These hairs are later sheared to equal lengths. A layer of puffy-like foam material is however placed under the embroidery material for the temporary fixing of the threads.
What is the technical difference between the TuftMaster and an embroidery machine?
Primarily, the cylinder arm of the normal embroidery machine is replaced by a new special unit. This device cuts the loop developed when penetrating the fabric so that two loose ends emerge. They form the basis for the soft pile.
The embroidery head shows two further modifications. As no bobbin thread is required for the StitchTuft process, the traditional thread take-up lever unit is not required. Furthermore, the upper thread monitor and the thread tension unit are modified, because the thread tension is very low in case of StitchTuft. What is the maximum height of the pile? The height of the pile depends on the height of the foam placed under the embroidery material. At first sight, this thin PE foam layer looks like the "Puffy" used for 3D embroidery. It has two functions. First, it fixes the inserted threads in position. But for this purpose, the PE foam must be more rubber-like than usual "Puffy". To keep the yarn in its position, the foam has to contract after stitching and hold the thread. In addition, the pile height depends on the height of the foam. As the threads are cut to the height of the "Puffy", the pile of the StitchTuft depends on the thickness of the "Puffy" - normally 2 to 5 mm.How do you fix the StitchTuft?
Before the foam layer can be stripped off and the finished StitchTuft appears, the threads which are first kept only by the "Puffy", must be fixed on the backside. For this purpose, the threads are bonded on the backside. Depending on the later use of the fabric, different methods are applied. At present, best results are achieved with a fusible adhesive. If the condition of the backside of the fabric is not important, adhesive films or glue powder can for example be used. Can StitchTuft be washed?
Yes, fabric with StitchTuft finish can be washed at 40°C. The strength of the pile and fixing are not affected thereby. Dry-cleaning is also possible.Can StitchTuft be ironed?
The StitchTuft finished areas on the face and backside of the fabric should not be ironed.
Can StitchTuft be dried in the tumble-dryer?This is possible, too. But as in case of all other textiles, the durability of the fabric is shortened by the thermal and mechanic stress.
How much yarn is consumed?
In case of StitchTuft, the yarn consumption is significantly higher than in traditional embroidery. The normal stitch length of the StitchTuft is about 1 mm. The yarn consumption amounts to approximately 25 mm. In normal embroidery, only 1.6 mm of yarn are required for the 1 mm stitch.
Do you use a special yarn?
Polyester yarn is most suitable.
How many stitches are made per minute?
At present, up to 850 stitches/minute are made.
Do you need a special shearing machine?
A powerful, high-performance shearing machine should be used which does not clog caused by the high amount of cut yarn ends. At present, we use an industrial shearing machine which on request, we can offer to you.
Is special maintenance/cleaning required due to the high amount of cut yarn ends?
The special unit of the machine should be cleaned at regular intervals to ensure the smooth operation.
Is a later fitting of the StitchTuft unit possible?
In theory, this is possible, but not realized in practice, i.e. always a new machine has to be purchased.
What is the maximum number of heads of the StitchTuft machine?
At present, machines with up to four heads are planned.
Do you need a special punching program for StitchTuft?
No, any customary punching program can be used.